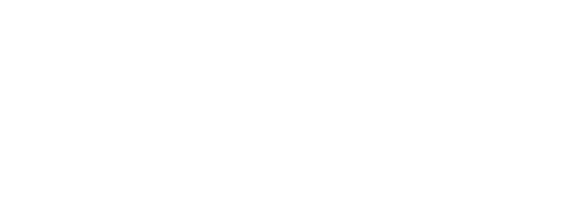
Langjährige Erfahrungen auf dem
Gebiet des Holzschutzes!
Gebiet des Holzschutzes!

Interessantes in Sachen Holzschutz
Holzschutzmittelschaumverfahren
Unter Mitwirkung von Herrn Nieke wurde an der TU Dresden im Auftrag der damaligen DESOWAG GmbH, Forschungs- und Entwicklungszentrum Krefeld, ein Schaumgerät entwickelt.
Nachdem der langjährige Hersteller, die Fa. Mäser in Freital bei Dresden aus Altersgründen die Herstellung eingestellt hatte, ist es gelungen, einen neuen Hersteller zu gewinnen.
Das Gerät wird voraussichtlich ab dem IV. Quartal des Jahres 2023 wieder lieferbar sein.
Es wird hergestellt durch die Fa. NIKRO Radeburg GmbH
Ansprechpartner Stefan Richter
Tel. +49 35208 3422-111
Fax +49 35208 3422-222
Mail stefan.richter@nikro.de
Web www.nikro-stahlbau.de
NIKRO Radeburg GmbH
Pfälzer Allee 3
D-01471 Radeburg
Natürlich stehen wir Ihnen auch weiterhin für Rückfragen unter info@holzschutz-nieke.de zur Verfügung.
Holzschutzmittel mit dem Schaumverfahren umweltbewusst und sicher anwenden
AUSGANGSPUNKT: Das Holzschutzmittelschaumverfahren ist keine neue Erfindung. Seine Ursprünge reichen bis in die fünfziger Jahre zurück. Von 1973 bis 1975 wurde das Verfahren von Chem.-Ing. Heinz Petermann (Berlin) soweit entwickelt, dass ein praktischer Einsatz möglich war.
Der Ausgangspunkt war die Unzufriedenheit über Aerosolbelastung beim Spritzen von Holzschutzmitteln. Außerdem genügte die Einbringmenge eines Arbeitsganges beim Streichen nicht, ein hoher Arbeitsaufwand war die Folge. Beim Fluten von Mauerwerk sind die Verluste sehr hoch und die Beeinträchtigung darunterliegender Bereiche nicht ohne Bedeutung.
IDEE: Das führte zu folgender Idee als Grundgedanke zum Verfahren:
Das Holzschutzmittel, welches aufschäumbar sein muss (ggf. durch
Tensidzusatz) wird in eine Schaumphase überführt.
Dieser Schaum wird auf die zu behandelnde Oberfläche (Holz oder
Mauerwerk) aufgetragen.
Durch den Schaumzerfall wird das Holzschutzmittel langsam
freigesetzt. Dabei ist die Zerfallskinetik so eingestellt, dass pro
Zeiteinheit nur so viel Tränkmittel an der Grenzfläche Schaum/Bauteil frei wird, wie die Oberfläche aufnehmen kann. Zum anderen soll der Schaum an der Grenzfläche zur Umgebungsluft möglichst stabil sein.
ZIEL: Das Ziel des Verfahrens besteht im Erreichen des notwendigen chemischen Schutzes bei:
1) Verringerung von Aerosolbelastung und Abtropfverlusten gegenüber dem Spritzen, Sprühen bzw. Fluten, damit ist das Verfahren umwelt- und arbeitsschutzfreundlicher,
2) Verringerung des Arbeitsaufwandes, ein Arbeitsgang ist ausreichend, die Eindringtiefe erhöht sich durch das langsame Eindringen, damit ist das Verfahren effektiver,
3) Vermeidung der Beeinträchtigung nicht zu behandelnder Bauteile durch das Fluten, damit ist das Verfahren anwenderfreundlicher und
4) Verbesserung der Erreichbarkeit von schwer zugänglichen Bauteilen (z. B. Unterdielenräume, freigestemmte Balkenköpfe, zweischaliges Mauerwerk), damit ist das Verfahren sicherer.
Bis 1989 wurden verschiedene Gerätekombinationen entwickelt und in geringem Umfang eingesetzt. Man unterschied das passive Verfahren nach Petermann und das aktive Verfahren nach Kluck und Schneevogt /10/.
Beim passiven Verfahren wird der Schaum in einem stationären Behälter erzeugt. Vorteile dieses Verfahrens sind die Kompaktheit des Gerätes und die Handhabbarkeit des Schaumschlauches. Nachteilig ist die diskontinuierliche Arbeitsweise und die beschränkte Regulierbarkeit von Schaummenge und -konsistenz. Außerdem führt der Einsatz eines Druckbehälters noch dazu bei der Befüllung mit Gefahrstoffen zu hohen Kosten.
Beim aktiven Verfahren erfolgt die Schaumerzeugung in einem Mischrohr direkt vor dem Auftrag. Vorteilhaft ist dabei die Regulierbarkeit der Schaumeigenschaften und die kontinuierliche Arbeitsweise, nachteilig das Mitführen von zwei Schläuchen und die im Schäumrohr vorhandenen Siebflächen. Außerdem wird der Schaum aus einer geringen Entfernung auf das Bauteil geschleudert, was zwar effektiv ist und ggf. die Haftung des Schaumes verbessert, jedoch kommt es dabei auch zum Umherfliegen von Schaumfetzen und damit zu erhöhter Aerosolbildung.
Verschiedene Untersuchungen zum Verfahren selbst als auch zur Wirkung des Tensides auf die Holzschutzmittel und auf die Wegbarkeit wurden u.a. in Eberswalde durchgeführt. In den Baureparaturbetrieben Berlin – Prenzlauer Berg und Mitte wurden Werkstandards zum Holzschutzmittelschaumverfahren entwickelt. In der Bauzeitung erschienen verschiedene Veröffentlichungen (s. Literaturverzeichnis). Im Januar 1990 lag bereits ein TGL-Entwurf zum Schaumverfahren vor. Als Holzschutzmittel wurde hauptsächlich Dohnalit Ull eingesetzt. Die unter den wirtschaftlichen Bedingungen der DDR zur Verfügung stehende Gerätetechnik und die begrenzten Schäumfähigkeit von Dohnalit Ull hinderten das Verfahren jedoch an einer weiteren Verbreitung.
In den Altbundesländern war das Verfahren weitgehend unbekannt, stieß aber nach 1989 auf Interesse, so auch bei der DESOWAG GmbH Düsseldorf. Es kam ein Forschungsvertrag zwischen dem Forschungs- und Entwicklungszentrum des Unternehmens und dem Institut für Holz- und Papiertechnik der TU Dresden zustande, der die Entwicklung einer geeigneten Gerätetechnik und Untersuchungen zur Eignung verschiedener Holzschutzmittel und Tenside beinhaltete. Ziel war es, die Probleme der bisher bekannten Gerätekombinationen zu lösen und das Verfahren und die Handhabbarkeit der Gerätetechnik einfacher, sicherer und zuverlässiger zu gestalten.
Im Ergebnis der Entwicklungsarbeit entstand ein Gerät, welches die Vorteile beider vorgenannten Verfahren vereint. Der Schaum wird stationär und kontinuierlich in der gewünschten Konzentration erzeugt. Der Verarbeiter hat nur einen Dreiviertelzoll-Schlauch und eine leichte Kunststoffdüse zu führen. Der Schaum wird ohne Abstand direkt auf das betreffende Bauteil aufgebracht, dadurch entstehen keinerlei Verluste oder Belastungen des Arbeitsumfeldes. Mittels eines Kugelhahnes an der Düse kann der Schaumstrom unterbrochen werden. Die Düse kann je nach Anwendungszweck verschieden breit sein und ist leicht auswechselbar. Die Schaumqualität und -menge wird über die Fördermenge der Pumpe und über den Luftdruck geregelt. Als Energie wird nur Druckluft benötigt, welche auch von einem vorhandenen Kompressor bezogen werden kann, da zur Förderung des Tränkmittels eine luftgetriebene Membranpumpe dient. Es genügt dabei ein handelsüblicher Kompressor mit einer Fördermenge von 220 Liter Luft pro Minute und 6 bar Druck. Dieser Kompressor kann auch in beliebiger Entfernung vom Schaumgerät (je nach Länge des verfügbaren Druckschlauches) stehen (z.B. auch außerhalb der Baustelle).
Die Einzelteile des Gerätes sind wartungs- und transportfreundlich (größte Einzelmasse: Kompressor). Das Hauptaggregat – die Pumpe mit dem Schaumrohr und den Regeleinrichtungen – wiegt 5 kg. Als Tränkmittelvorratsbehälter kann jedes baustellenübliche Gefäß (Eimer, Kanister usw.) verwendet werden. Baustellentypische Verunreinigungen (z.B. Sand) stören nicht, sie werden durch ein Sieb im Ansaugstutzen ferngehalten. Ein weiterer wesentlicher Vorteil des Gerätes ist die Verwendung von Druckluft zur Schaumerzeugung. Der so erzeugte Schaum enthält einen gewissen Eigendruck und kann so problemlos zum Ausschäumen von Hohlräumen eingesetzt werden. Der Schaum wird dabei z.B. durch Unterdielenräume oder zweischaliges Mauerwerk geschoben. Im Rastermaß von 1,5 m wird der zu behandelnde Hohlraum mit einem Bohrungsdurchmesser von 25 mm angebohrt. Eine spezielle, konische Hohlraumdüse wird in die Bohrung eingepresst und der Verschäumvorgang kann beginnen. Wichtig ist dabei die Kenntnis der Schaumkonsistenz (s. u.). Es konnte nachgewiesen werden, dass über eine Strecke von mindestens 1,5 m der Schaum keinerlei Veränderungen bezüglich der Konsistenz erfährt /1/.
Die wesentlichen Bestandteile des Verschäumgerätes sind:
1) Kompressor mit folgenden Anforderungen:
Überdruck: 6 bar | Ansaugvolumen: 300 Liter/min | Ausgang möglichst mit Druckminderer und handelsüblicher Schnellkupplung | beliebig langer Druckluftschlauch
2) Schaumgerät bestehend aus:
- Druckluftgetriebener Doppelmembranpumpe Wilden M-025 aus Kunststoff (PP, Masse 1,1 kg, stufenlos regelbar mittels Druckminderer)
- Schaumrohr als Kernstück der Anlage. Es wurde zum Patent angemeldet. Auf einem Grundkörper mit entsprechenden Anschlussstutzen für Luft- und Tränkmittelschlauch befinden sich zwei Rohre ineinander, von welchem das innere perforiert ist. Durch diese Perforierung wird die Luft in den das Rohr umströmenden Tränkmittelmantel gepresst und dieses somit verschäumt. Die senkrechte Anordnung des Rohres führt zu einer gleichmäßigeren Schaumqualität, da unverschäumte Tränkmittelanteile im Rohr unten bleiben. Am oberen Ende des Schaumrohres liegt fertiger Schaum vor. Der Anschluss für den Schaumschlauch (3/4") wurde wieder nach unten gezogen, um die Standsicherheit des Gerätes bei Zug am Schaumschlauch zu verbessern. Material und Konstruktion des Schaumrohres sind chemikalien- und druckbeständig.
- Regel- und Bedieneinrichtungen:
Anschlussstutzen für Druckluftschlauch, Hauptabsperrhahn, 2 Druckminderer mit Manometer für Schaumluft und Doppelmembranpumpe, Ansaugschlauch mit Gewicht und Filter
3) Schaumschlauch und Austragsdüse(n) mit Kugelhahn:
Die Austragsdüsen dienen zum Aufbringen des Schaumes auf das entsprechende Bauteil. Daher sind Düsen in verschiedenen Dimensionen sinnvoll. Breite für großflächige Bauteile (z.B. Schalungen und Mauerwerk), schmale für kleinflächige Bauteile (z. B. für Sparren) und kleine runde, konische Düse zum Verfüllen von Hohlräumen bzw. zum Aufspritzen des Schaumes. Die Länge der Düsen kann ebenfalls dem Einsatzzweck angepasst werden. Die Düsen sind leicht lösbar mit einem Kugelhahn verbunden. Dieser dient zum Sperren des Schaumstromes. Material und Konstruktion der Düsen und des Kugelhahnes sind chemikalien- und druckbeständig. Zur Masseverringerung wurde eine Ausführung in Kunststoff gewählt.
Bezüglich der einzusetzenden Holzschutzmittel interessierten vor allem Mittel zur Bekämpfung von Hausschwamm im Mauerwerk und zur vorbeugenden Behandlung verbauten Holzes, z.B. nach der Heißluftbehandlung.
Dabei hat sich Basilit M der Fa. DESOWAG (auf der Basis quartanärer Ammoniumverbindungen) wegen der universellen Einsetzbarkeit (Behandlung von Mauerwerk gegen Echten Hausschwamm und von Holz vorbeugend gegen Pilze /12/) und des Eigenschäumvermögens ohne Tensidzusatz am besten bewährt.
Inzwischen ist auch die Bekämpfung von Insekten im Holz durch das Schaumverfahren möglich. Fast alle namhaften deutschen Holzschutzmittelhersteller haben mittlerweile Mittel für den Einsatz im Schaumverfahren modifiziert und geprüft.
Denkbar ist auch der Einsatz zum Erstschutz an verbautem Holz. Das wäre ein weiterer Schritt in Richtung Minimierung des Holzschutzmitteleinsatzes: Am rohbaufertigen Bau können z. B. nur die Teile eines Dachstuhles mit einem Borprodukt beschäumt werden, die nicht der Gefährdungsklasse 0 zuzuordnen sind (Fußpfetten, Sparrenfuß- und Firstpunkte usw.). Dazu wäre die Zulassung von DIBt-geprüften Holzschutzmitteln notwendig.
Darüber hinaus laufen gegenwärtig Untersuchungen zum Einsatz des Schaumverfahrens im Bautenschutzbereich, z. B. zum Auftragen von Hydrophobierungsmitteln und (Fassaden)reinigungsmitteln.
Laut einer Stellungnahme des Umweltbundesamtes vom Mai 1992 „... kann das Holzschutzmittelschaumverfahren grundsätzlich als umweltfreundliche Alternative zum Spritzverfahren ... unter Dach in Betracht gezogen werden.“
Die wichtigste Kenngröße des Schaumes ist das Tränkmittel-Schaum-Verhältnis (im folgenden mit TSV bezeichnet). Es gibt an, wieviel Tränkmittelvolumen pro Schaumvolumen enthalten ist. Ein TSV von z. B. 1:30 bedeutet, dass 1 Liter Tränkmittel zu 30 Litern Schaum aufgeschäumt wird.
Es ist nicht das Ziel, ein möglichst großes TSV zu erreichen, denn für Zerfallszeit und Stabilität des Schaumes ist auch die Porengröße und -anzahl entscheidend. Ein feinporiger Schaum ist wesentlich stabiler als ein Schaum mit großen Poren (und somit großem TSV). Außerdem ist bei einem hohen TSV auch eine größere Schaumschichtdicke erforderlich, was wiederum das Haftungsvermögen des Schaumes beeinflusst.
Dieses Tränkmittel-Schaum-Verhältnis kann am Schaumgerät von DESOWAG durch die einfache Regulierbarkeit von Tränkmittel- und Luftstrom in den durch das Schaumvermögen des Holzschutzmittels vorgegebenen Grenzen beliebig variiert werden, ebenso die erzeugte Schaummenge pro Zeiteinheit. Die Überprüfung des Tränkmittel-Schaum-Verhältnisses kann sehr einfach durchgeführt werden. Ein Gefäß mit bekanntem Volumen (z.B. 5-l-Wassereimer) wird mit Schaum gefüllt. Die Krone wird abgestrichen. Nach dem Zerfall des Schaumes kann die Tränkmittelmenge mittels Mensur bestimmt werden. Es wurde nachgewiesen, dass diese Methode hinreichend genau ist /11/.
Die Berechnung der notwendigen Schaumhöhe ist bei Kenntnis des Tränkmittelschaumverhältnisses kein Problem.
Prinzipiell wird den Anwendern empfohlen, nur Mittel einzusetzen, die per RAL-Urkunde bzw. bauaufsichtlicher Zulassung zum Schäumen ausgeworben sind. Dabei sind nur Tenside einzusetzen, die mit dem entsprechenden Holzschutzmittel geprüft wurden. Alle „Eigenversuche“ mit Tensiden (Geschirrspülmittel etc.) können u. a. zu Gewährleistungsproblemen führen, da die Zusammensetzung des Mittels sich dann von der geprüften unterscheidet.
Natürlich ist das Verfahren kein „Allheilmittel“. Es ist darauf hinzuweisen, dass zwar eine größere Eindringtiefe erreicht wird als beim Fluten oder Sprühen, jedoch das Verfahren kein Ersatz für die lt. DIN 68 800 T4 bzw. WTA-Merkblatt „Der Echte Hausschwamm“ bei Mauerstärken über 20 cm vorzunehmende Injektage des Mauerwerkes ist.
Der Einsatz des Schaumverfahrens kann nur durch Fachfirmen erfolgen. Zum einen gebietet dies schon der lt. Gefahrenstoffverordnung geregelte Umgang mit bekämpfenden Holzschutzmitteln, zum anderen ist im Umgang mit der Gerätetechnik eine gewisse Erfahrung notwendig.
Ein anwendungstechnisches Problem stellen staubige Oberflächen dar. Diese müssen zur besseren Haftung des Schaumes gereinigt werden, da sich der Schaum sonst schichtartig mit dem Staub löst. Dabei ist es sinnvoll, die Flächen bei der Reinigung vorzunässen, z. B. durch das Abkehren mit einem feuchten Besen.
Beim Arbeiten mit dem Schaumgerät ist die übliche Arbeitsschutzkleidung (wasserdichte Kleidung, Handschuhe, Brille, Nackenschutz usw.) erforderlich.
Die MAK-Werte sind noch nicht ermittelt worden. Sie sind aber mit Sicherheit geringer, als beim Spritzen bzw. Fluten, das ist z.B. bei der Verarbeitung quartanärer Ammoniumverbindungen schon an der verminderten Geruchsbelastung deutlich zu spüren.
In einer Stellungnahme des Bundesgesundheitsamtes vom Juni 1992 heißt es: „... das Holzschutzmittelschaumverfahren soll die Nachteile des Spritzverfahrens minimieren bzw. beseitigen und als alternatives Einbringverfahren für Holzschutzmittel in den alten Bundesländern eingeführt werden.“
Resümee:
Europaweit werden z. Z. mehr als 200 Geräte dieser Bauart von Holz- und Bautenschutzunternehmen mit den verschiedensten Mitteln eingesetzt. Es zeigt sich, dass die vier für die Entwicklung des Schaumverfahrens gesteckten Ziele
- arbeitsschutz- und umweltfreundlicher
- effektiver
- anwenderfreundlicher
- sicherer
mit diesem Gerät durchaus erreicht werden. Entsprechend dem Trend, den Einsatz biozider Chemikalien zu minimieren bzw. zu optimieren, ist das Schaumverfahren ein wichtiger Beitrag zur Anwendungssicherheit und Reduzierung der Umweltbelastung vor allem während der Verarbeitung.
Literatur:
/1/ Fischer, H: Untersuchungen zur Eignung des Holzschutzmittelschaumverfahrens zur Behandlung von Hohlräumen, Diplomarbeit TU Dresden, 1995
/2/ Flint, E., Roßkopf, W.: Schwammsanierung – Alte Pracht in neuem Glanz, in Bautenschutz Bausanierung, Heft 1/98
/3/ Kluck, R., Schneevogt, J., Erdmann, E.: Weitere Untersuchungen zum Holzschutzmittelschaumverfahren, in Bauzeitung Jg. 40, Heft 10 Berlin 1986
/4/ Kluck, R., Schneevogt, J., Reifenstein, Dr. H., Pätzold, M.: Holzschutzmittelschaumverfahren – technologische Erfahrungen und arbeitshygienische Bewertung, in Bauzeitung Jg. 41, Heft 3 Berlin 1987
/5/ Krotki, L.-H., Kluck, R., Schneevogt, J.: Holzschutzmittelschaumverfahren – gerätetechnische Entwicklung und erste Ergebnisse bei der Anwendung, in Bauzeitung Jg. 40, Heft 4 Berlin 1986
/6/ Petermann, H.: Holzschutzmittelschaumverfahren, in Bauzeitung Jg. 29, Heft 9 Berlin 1975
/7/ Rafalski, Dr. H.-J.; Biering B.: Holzschutz-Beschäumverfahren – Die ökologische Alternative zum Spritzverfahren, Leipziger Gesellschaft für Bausanierung mbH, Leipzig 1990
/8/ Rafalski, Dr. H.-J.: Das Holzschutz-Schaumverfahren im Vergleich von Ökologie, Ökonomie und Effektivität, in Tagungsunterlagen GSG-Seminare, Mühlenbeck, September 1998
/9/ Roßkopf, W.: Das Holzschutzmittelschaumverfahren – Eine umwelt- und verarbeiterfreundliche Alternative, in Holzschutzimpulse 34, Düsseldorf August 1995
/10/ Schneevogt, J.: Technik, Anwendung und Demonstration des Holzschutz-Beschäumverfahrens, in Tagungsunterlagen Holzschutz in ACTION, Berlin, September 1993
/11/ Wuttke, M: Untersuchungen zum Einsatz des Holzschutzmittelschaumverfahrens, Diplomarbeit TU Dresden, 1994
/12/ Technisches Merkblatt zu Basilieum M, DESOWAG GmbH
Holzschutzmittelschaumverfahren
Unter Mitwirkung von Herrn Nieke wurde an der TU Dresden im Auftrag der damaligen DESOWAG GmbH, Forschungs- und Entwicklungszentrum Krefeld, ein Schaumgerät entwickelt.
Nachdem der langjährige Hersteller, die Fa. Mäser in Freital bei Dresden aus Altersgründen die Herstellung eingestellt hatte, ist es gelungen, einen neuen Hersteller zu gewinnen.
Das Gerät wird voraussichtlich ab dem IV. Quartal des Jahres 2023 wieder lieferbar sein.
Es wird hergestellt durch die Fa. NIKRO Radeburg GmbH
Ansprechpartner Stefan Richter
Tel. +49 35208 3422-111
Fax +49 35208 3422-222
Mail stefan.richter@nikro.de
Web www.nikro-stahlbau.de
NIKRO Radeburg GmbH
Pfälzer Allee 3
D-01471 Radeburg
Natürlich stehen wir Ihnen auch weiterhin für Rückfragen unter info@holzschutz-nieke.de zur Verfügung.
Holzschutzmittel mit dem Schaumverfahren umweltbewusst und sicher anwenden
AUSGANGSPUNKT: Das Holzschutzmittelschaumverfahren ist keine neue Erfindung. Seine Ursprünge reichen bis in die fünfziger Jahre zurück. Von 1973 bis 1975 wurde das Verfahren von Chem.-Ing. Heinz Petermann (Berlin) soweit entwickelt, dass ein praktischer Einsatz möglich war.
Der Ausgangspunkt war die Unzufriedenheit über Aerosolbelastung beim Spritzen von Holzschutzmitteln. Außerdem genügte die Einbringmenge eines Arbeitsganges beim Streichen nicht, ein hoher Arbeitsaufwand war die Folge. Beim Fluten von Mauerwerk sind die Verluste sehr hoch und die Beeinträchtigung darunterliegender Bereiche nicht ohne Bedeutung.
IDEE: Das führte zu folgender Idee als Grundgedanke zum Verfahren:
Tensidzusatz) wird in eine Schaumphase überführt.
Mauerwerk) aufgetragen.
freigesetzt. Dabei ist die Zerfallskinetik so eingestellt, dass pro
Zeiteinheit nur so viel Tränkmittel an der Grenzfläche Schaum/Bauteil frei wird, wie die Oberfläche aufnehmen kann. Zum anderen soll der Schaum an der Grenzfläche zur Umgebungsluft möglichst stabil sein.
1) Verringerung von Aerosolbelastung und Abtropfverlusten gegenüber dem Spritzen, Sprühen bzw. Fluten, damit ist das Verfahren umwelt- und arbeitsschutzfreundlicher,
2) Verringerung des Arbeitsaufwandes, ein Arbeitsgang ist ausreichend, die Eindringtiefe erhöht sich durch das langsame Eindringen, damit ist das Verfahren effektiver,
3) Vermeidung der Beeinträchtigung nicht zu behandelnder Bauteile durch das Fluten, damit ist das Verfahren anwenderfreundlicher und
4) Verbesserung der Erreichbarkeit von schwer zugänglichen Bauteilen (z. B. Unterdielenräume, freigestemmte Balkenköpfe, zweischaliges Mauerwerk), damit ist das Verfahren sicherer.
Bis 1989 wurden verschiedene Gerätekombinationen entwickelt und in geringem Umfang eingesetzt. Man unterschied das passive Verfahren nach Petermann und das aktive Verfahren nach Kluck und Schneevogt /10/.
Beim passiven Verfahren wird der Schaum in einem stationären Behälter erzeugt. Vorteile dieses Verfahrens sind die Kompaktheit des Gerätes und die Handhabbarkeit des Schaumschlauches. Nachteilig ist die diskontinuierliche Arbeitsweise und die beschränkte Regulierbarkeit von Schaummenge und -konsistenz. Außerdem führt der Einsatz eines Druckbehälters noch dazu bei der Befüllung mit Gefahrstoffen zu hohen Kosten.
Beim aktiven Verfahren erfolgt die Schaumerzeugung in einem Mischrohr direkt vor dem Auftrag. Vorteilhaft ist dabei die Regulierbarkeit der Schaumeigenschaften und die kontinuierliche Arbeitsweise, nachteilig das Mitführen von zwei Schläuchen und die im Schäumrohr vorhandenen Siebflächen. Außerdem wird der Schaum aus einer geringen Entfernung auf das Bauteil geschleudert, was zwar effektiv ist und ggf. die Haftung des Schaumes verbessert, jedoch kommt es dabei auch zum Umherfliegen von Schaumfetzen und damit zu erhöhter Aerosolbildung.
Verschiedene Untersuchungen zum Verfahren selbst als auch zur Wirkung des Tensides auf die Holzschutzmittel und auf die Wegbarkeit wurden u.a. in Eberswalde durchgeführt. In den Baureparaturbetrieben Berlin – Prenzlauer Berg und Mitte wurden Werkstandards zum Holzschutzmittelschaumverfahren entwickelt. In der Bauzeitung erschienen verschiedene Veröffentlichungen (s. Literaturverzeichnis). Im Januar 1990 lag bereits ein TGL-Entwurf zum Schaumverfahren vor. Als Holzschutzmittel wurde hauptsächlich Dohnalit Ull eingesetzt. Die unter den wirtschaftlichen Bedingungen der DDR zur Verfügung stehende Gerätetechnik und die begrenzten Schäumfähigkeit von Dohnalit Ull hinderten das Verfahren jedoch an einer weiteren Verbreitung.
In den Altbundesländern war das Verfahren weitgehend unbekannt, stieß aber nach 1989 auf Interesse, so auch bei der DESOWAG GmbH Düsseldorf. Es kam ein Forschungsvertrag zwischen dem Forschungs- und Entwicklungszentrum des Unternehmens und dem Institut für Holz- und Papiertechnik der TU Dresden zustande, der die Entwicklung einer geeigneten Gerätetechnik und Untersuchungen zur Eignung verschiedener Holzschutzmittel und Tenside beinhaltete. Ziel war es, die Probleme der bisher bekannten Gerätekombinationen zu lösen und das Verfahren und die Handhabbarkeit der Gerätetechnik einfacher, sicherer und zuverlässiger zu gestalten.
Im Ergebnis der Entwicklungsarbeit entstand ein Gerät, welches die Vorteile beider vorgenannten Verfahren vereint. Der Schaum wird stationär und kontinuierlich in der gewünschten Konzentration erzeugt. Der Verarbeiter hat nur einen Dreiviertelzoll-Schlauch und eine leichte Kunststoffdüse zu führen. Der Schaum wird ohne Abstand direkt auf das betreffende Bauteil aufgebracht, dadurch entstehen keinerlei Verluste oder Belastungen des Arbeitsumfeldes. Mittels eines Kugelhahnes an der Düse kann der Schaumstrom unterbrochen werden. Die Düse kann je nach Anwendungszweck verschieden breit sein und ist leicht auswechselbar. Die Schaumqualität und -menge wird über die Fördermenge der Pumpe und über den Luftdruck geregelt. Als Energie wird nur Druckluft benötigt, welche auch von einem vorhandenen Kompressor bezogen werden kann, da zur Förderung des Tränkmittels eine luftgetriebene Membranpumpe dient. Es genügt dabei ein handelsüblicher Kompressor mit einer Fördermenge von 220 Liter Luft pro Minute und 6 bar Druck. Dieser Kompressor kann auch in beliebiger Entfernung vom Schaumgerät (je nach Länge des verfügbaren Druckschlauches) stehen (z.B. auch außerhalb der Baustelle).
Die Einzelteile des Gerätes sind wartungs- und transportfreundlich (größte Einzelmasse: Kompressor). Das Hauptaggregat – die Pumpe mit dem Schaumrohr und den Regeleinrichtungen – wiegt 5 kg. Als Tränkmittelvorratsbehälter kann jedes baustellenübliche Gefäß (Eimer, Kanister usw.) verwendet werden. Baustellentypische Verunreinigungen (z.B. Sand) stören nicht, sie werden durch ein Sieb im Ansaugstutzen ferngehalten. Ein weiterer wesentlicher Vorteil des Gerätes ist die Verwendung von Druckluft zur Schaumerzeugung. Der so erzeugte Schaum enthält einen gewissen Eigendruck und kann so problemlos zum Ausschäumen von Hohlräumen eingesetzt werden. Der Schaum wird dabei z.B. durch Unterdielenräume oder zweischaliges Mauerwerk geschoben. Im Rastermaß von 1,5 m wird der zu behandelnde Hohlraum mit einem Bohrungsdurchmesser von 25 mm angebohrt. Eine spezielle, konische Hohlraumdüse wird in die Bohrung eingepresst und der Verschäumvorgang kann beginnen. Wichtig ist dabei die Kenntnis der Schaumkonsistenz (s. u.). Es konnte nachgewiesen werden, dass über eine Strecke von mindestens 1,5 m der Schaum keinerlei Veränderungen bezüglich der Konsistenz erfährt /1/.
Die wesentlichen Bestandteile des Verschäumgerätes sind:
1) Kompressor mit folgenden Anforderungen:
Überdruck: 6 bar | Ansaugvolumen: 300 Liter/min | Ausgang möglichst mit Druckminderer und handelsüblicher Schnellkupplung | beliebig langer Druckluftschlauch
2) Schaumgerät bestehend aus:
- Druckluftgetriebener Doppelmembranpumpe Wilden M-025 aus Kunststoff (PP, Masse 1,1 kg, stufenlos regelbar mittels Druckminderer)
- Schaumrohr als Kernstück der Anlage. Es wurde zum Patent angemeldet. Auf einem Grundkörper mit entsprechenden Anschlussstutzen für Luft- und Tränkmittelschlauch befinden sich zwei Rohre ineinander, von welchem das innere perforiert ist. Durch diese Perforierung wird die Luft in den das Rohr umströmenden Tränkmittelmantel gepresst und dieses somit verschäumt. Die senkrechte Anordnung des Rohres führt zu einer gleichmäßigeren Schaumqualität, da unverschäumte Tränkmittelanteile im Rohr unten bleiben. Am oberen Ende des Schaumrohres liegt fertiger Schaum vor. Der Anschluss für den Schaumschlauch (3/4") wurde wieder nach unten gezogen, um die Standsicherheit des Gerätes bei Zug am Schaumschlauch zu verbessern. Material und Konstruktion des Schaumrohres sind chemikalien- und druckbeständig.
- Regel- und Bedieneinrichtungen:
Anschlussstutzen für Druckluftschlauch, Hauptabsperrhahn, 2 Druckminderer mit Manometer für Schaumluft und Doppelmembranpumpe, Ansaugschlauch mit Gewicht und Filter
3) Schaumschlauch und Austragsdüse(n) mit Kugelhahn:
Die Austragsdüsen dienen zum Aufbringen des Schaumes auf das entsprechende Bauteil. Daher sind Düsen in verschiedenen Dimensionen sinnvoll. Breite für großflächige Bauteile (z.B. Schalungen und Mauerwerk), schmale für kleinflächige Bauteile (z. B. für Sparren) und kleine runde, konische Düse zum Verfüllen von Hohlräumen bzw. zum Aufspritzen des Schaumes. Die Länge der Düsen kann ebenfalls dem Einsatzzweck angepasst werden. Die Düsen sind leicht lösbar mit einem Kugelhahn verbunden. Dieser dient zum Sperren des Schaumstromes. Material und Konstruktion der Düsen und des Kugelhahnes sind chemikalien- und druckbeständig. Zur Masseverringerung wurde eine Ausführung in Kunststoff gewählt.
Bezüglich der einzusetzenden Holzschutzmittel interessierten vor allem Mittel zur Bekämpfung von Hausschwamm im Mauerwerk und zur vorbeugenden Behandlung verbauten Holzes, z.B. nach der Heißluftbehandlung.
Dabei hat sich Basilit M der Fa. DESOWAG (auf der Basis quartanärer Ammoniumverbindungen) wegen der universellen Einsetzbarkeit (Behandlung von Mauerwerk gegen Echten Hausschwamm und von Holz vorbeugend gegen Pilze /12/) und des Eigenschäumvermögens ohne Tensidzusatz am besten bewährt.
Inzwischen ist auch die Bekämpfung von Insekten im Holz durch das Schaumverfahren möglich. Fast alle namhaften deutschen Holzschutzmittelhersteller haben mittlerweile Mittel für den Einsatz im Schaumverfahren modifiziert und geprüft.
Denkbar ist auch der Einsatz zum Erstschutz an verbautem Holz. Das wäre ein weiterer Schritt in Richtung Minimierung des Holzschutzmitteleinsatzes: Am rohbaufertigen Bau können z. B. nur die Teile eines Dachstuhles mit einem Borprodukt beschäumt werden, die nicht der Gefährdungsklasse 0 zuzuordnen sind (Fußpfetten, Sparrenfuß- und Firstpunkte usw.). Dazu wäre die Zulassung von DIBt-geprüften Holzschutzmitteln notwendig.
Darüber hinaus laufen gegenwärtig Untersuchungen zum Einsatz des Schaumverfahrens im Bautenschutzbereich, z. B. zum Auftragen von Hydrophobierungsmitteln und (Fassaden)reinigungsmitteln.
Laut einer Stellungnahme des Umweltbundesamtes vom Mai 1992 „... kann das Holzschutzmittelschaumverfahren grundsätzlich als umweltfreundliche Alternative zum Spritzverfahren ... unter Dach in Betracht gezogen werden.“
Die wichtigste Kenngröße des Schaumes ist das Tränkmittel-Schaum-Verhältnis (im folgenden mit TSV bezeichnet). Es gibt an, wieviel Tränkmittelvolumen pro Schaumvolumen enthalten ist. Ein TSV von z. B. 1:30 bedeutet, dass 1 Liter Tränkmittel zu 30 Litern Schaum aufgeschäumt wird.
Es ist nicht das Ziel, ein möglichst großes TSV zu erreichen, denn für Zerfallszeit und Stabilität des Schaumes ist auch die Porengröße und -anzahl entscheidend. Ein feinporiger Schaum ist wesentlich stabiler als ein Schaum mit großen Poren (und somit großem TSV). Außerdem ist bei einem hohen TSV auch eine größere Schaumschichtdicke erforderlich, was wiederum das Haftungsvermögen des Schaumes beeinflusst.
Dieses Tränkmittel-Schaum-Verhältnis kann am Schaumgerät von DESOWAG durch die einfache Regulierbarkeit von Tränkmittel- und Luftstrom in den durch das Schaumvermögen des Holzschutzmittels vorgegebenen Grenzen beliebig variiert werden, ebenso die erzeugte Schaummenge pro Zeiteinheit. Die Überprüfung des Tränkmittel-Schaum-Verhältnisses kann sehr einfach durchgeführt werden. Ein Gefäß mit bekanntem Volumen (z.B. 5-l-Wassereimer) wird mit Schaum gefüllt. Die Krone wird abgestrichen. Nach dem Zerfall des Schaumes kann die Tränkmittelmenge mittels Mensur bestimmt werden. Es wurde nachgewiesen, dass diese Methode hinreichend genau ist /11/.
Die Berechnung der notwendigen Schaumhöhe ist bei Kenntnis des Tränkmittelschaumverhältnisses kein Problem.
Prinzipiell wird den Anwendern empfohlen, nur Mittel einzusetzen, die per RAL-Urkunde bzw. bauaufsichtlicher Zulassung zum Schäumen ausgeworben sind. Dabei sind nur Tenside einzusetzen, die mit dem entsprechenden Holzschutzmittel geprüft wurden. Alle „Eigenversuche“ mit Tensiden (Geschirrspülmittel etc.) können u. a. zu Gewährleistungsproblemen führen, da die Zusammensetzung des Mittels sich dann von der geprüften unterscheidet.
Natürlich ist das Verfahren kein „Allheilmittel“. Es ist darauf hinzuweisen, dass zwar eine größere Eindringtiefe erreicht wird als beim Fluten oder Sprühen, jedoch das Verfahren kein Ersatz für die lt. DIN 68 800 T4 bzw. WTA-Merkblatt „Der Echte Hausschwamm“ bei Mauerstärken über 20 cm vorzunehmende Injektage des Mauerwerkes ist.
Der Einsatz des Schaumverfahrens kann nur durch Fachfirmen erfolgen. Zum einen gebietet dies schon der lt. Gefahrenstoffverordnung geregelte Umgang mit bekämpfenden Holzschutzmitteln, zum anderen ist im Umgang mit der Gerätetechnik eine gewisse Erfahrung notwendig.
Ein anwendungstechnisches Problem stellen staubige Oberflächen dar. Diese müssen zur besseren Haftung des Schaumes gereinigt werden, da sich der Schaum sonst schichtartig mit dem Staub löst. Dabei ist es sinnvoll, die Flächen bei der Reinigung vorzunässen, z. B. durch das Abkehren mit einem feuchten Besen.
Beim Arbeiten mit dem Schaumgerät ist die übliche Arbeitsschutzkleidung (wasserdichte Kleidung, Handschuhe, Brille, Nackenschutz usw.) erforderlich.
Die MAK-Werte sind noch nicht ermittelt worden. Sie sind aber mit Sicherheit geringer, als beim Spritzen bzw. Fluten, das ist z.B. bei der Verarbeitung quartanärer Ammoniumverbindungen schon an der verminderten Geruchsbelastung deutlich zu spüren.
In einer Stellungnahme des Bundesgesundheitsamtes vom Juni 1992 heißt es: „... das Holzschutzmittelschaumverfahren soll die Nachteile des Spritzverfahrens minimieren bzw. beseitigen und als alternatives Einbringverfahren für Holzschutzmittel in den alten Bundesländern eingeführt werden.“
Resümee:
Europaweit werden z. Z. mehr als 200 Geräte dieser Bauart von Holz- und Bautenschutzunternehmen mit den verschiedensten Mitteln eingesetzt. Es zeigt sich, dass die vier für die Entwicklung des Schaumverfahrens gesteckten Ziele
- arbeitsschutz- und umweltfreundlicher
- effektiver
- anwenderfreundlicher
- sicherer
mit diesem Gerät durchaus erreicht werden. Entsprechend dem Trend, den Einsatz biozider Chemikalien zu minimieren bzw. zu optimieren, ist das Schaumverfahren ein wichtiger Beitrag zur Anwendungssicherheit und Reduzierung der Umweltbelastung vor allem während der Verarbeitung.
Literatur:
/1/ Fischer, H: Untersuchungen zur Eignung des Holzschutzmittelschaumverfahrens zur Behandlung von Hohlräumen, Diplomarbeit TU Dresden, 1995
/2/ Flint, E., Roßkopf, W.: Schwammsanierung – Alte Pracht in neuem Glanz, in Bautenschutz Bausanierung, Heft 1/98
/3/ Kluck, R., Schneevogt, J., Erdmann, E.: Weitere Untersuchungen zum Holzschutzmittelschaumverfahren, in Bauzeitung Jg. 40, Heft 10 Berlin 1986
/4/ Kluck, R., Schneevogt, J., Reifenstein, Dr. H., Pätzold, M.: Holzschutzmittelschaumverfahren – technologische Erfahrungen und arbeitshygienische Bewertung, in Bauzeitung Jg. 41, Heft 3 Berlin 1987
/5/ Krotki, L.-H., Kluck, R., Schneevogt, J.: Holzschutzmittelschaumverfahren – gerätetechnische Entwicklung und erste Ergebnisse bei der Anwendung, in Bauzeitung Jg. 40, Heft 4 Berlin 1986
/6/ Petermann, H.: Holzschutzmittelschaumverfahren, in Bauzeitung Jg. 29, Heft 9 Berlin 1975
/7/ Rafalski, Dr. H.-J.; Biering B.: Holzschutz-Beschäumverfahren – Die ökologische Alternative zum Spritzverfahren, Leipziger Gesellschaft für Bausanierung mbH, Leipzig 1990
/8/ Rafalski, Dr. H.-J.: Das Holzschutz-Schaumverfahren im Vergleich von Ökologie, Ökonomie und Effektivität, in Tagungsunterlagen GSG-Seminare, Mühlenbeck, September 1998
/9/ Roßkopf, W.: Das Holzschutzmittelschaumverfahren – Eine umwelt- und verarbeiterfreundliche Alternative, in Holzschutzimpulse 34, Düsseldorf August 1995
/10/ Schneevogt, J.: Technik, Anwendung und Demonstration des Holzschutz-Beschäumverfahrens, in Tagungsunterlagen Holzschutz in ACTION, Berlin, September 1993
/11/ Wuttke, M: Untersuchungen zum Einsatz des Holzschutzmittelschaumverfahrens, Diplomarbeit TU Dresden, 1994
/12/ Technisches Merkblatt zu Basilieum M, DESOWAG GmbH
© Ingenieurbüro Holzschutz Nieke
2011-2025 | Datenschutz